How to Properly Evaluate & Compare Diamond Blade Performance
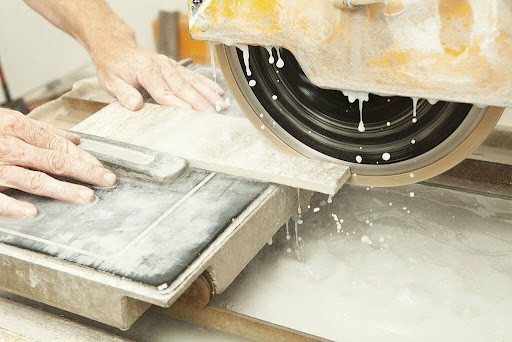
Diamond blades play a role, in industries such as construction and manufacturing serving as the tool for cutting through tough materials like concrete, asphalt and natural stone.
Selecting the diamond blade for an application can significantly impact both the efficiency and quality of the cutting process.
To ensure performance it is crucial to understand how to evaluate and compare the performance of diamond blades.
Material Compatibility
The first step in evaluating diamond blade performance involves understanding the materials they will be used to cut. Different blades are specifically designed for materials. Using an unsuitable blade can result in reduced efficiency and premature wear.
It’s important to consider factors such as hardness, abrasiveness, and composition in order to match them with the diamond blade. For the most reliable information and top-quality diamond blades, you must visit this site for the best selection
Diamond Grit Size
The size of diamond grit on the cutting edge is a factor that determines a blade’s performance. Larger grits are better suited for materials while smaller ones are effective for substances.
By understanding the grit size requirements, for each material being cut it ensures that the blade can efficiently grind through surfaces without wear.
Different Types of Bond
Diamond blades are available, in bond types that determine how well the diamond particles are held together. The choice of bond should match the hardness of the material you’re cutting.
For instance a soft bond is ideal for materials as it provides a more efficient cut. On the other hand a hard bond is better suited for materials as it offers durability and longevity.
Segmented Design
The design of a blade segment plays a role in achieving cutting results. Segmented rims are suitable when you need aggressive cuts while turbo rims are designed to provide cuts with minimal chipping.
If you’re working with materials that tend to chip continuous rim blades with their cutting edge would be your best bet.
Blade Diameter and RPM
Choosing the blade diameter and ensuring its compatibility with the equipment’s RPM (Revolutions Per Minute) is essential for optimal cutting performance.
Using a blade that matches the recommended diameter and RPM ensures both safety and efficiency. Deviating from the manufacturers guidelines can lead to decreased efficiency, increased wear on equipment and potential safety risks.
Water Usage
In wet cutting applications water is commonly used to cool down the blade and control dust levels. The ability of a diamond blade to manage water flow is crucial, for maintaining its performance while preventing overheating.
Blades that have good water dispersion features play a role in ensuring a cool cutting process.
Testing Performance
Before making a decision it is recommended to carry out performance tests.
By testing the diamond blade on a sample of the material you intend to cut you can evaluate its cutting speed, precision and overall efficiency. This hands on approach allows for an assessment of how well the blade performs under real world conditions.
Conclusion
Selecting the diamond blade for your cutting needs requires an understanding of the materials blade specifications and performance characteristics. By evaluating and comparing these factors users can choose a diamond blade that not meets their expectations but surpasses them in terms of efficiency, durability and precision.
In industries like construction and manufacturing where precision’s crucial investing time in selecting the diamond blade is an investment, in both performance and safety.